without context there is no information
Despite the enormous development in process automation recent decades, little has changed in HMI design with the result that the operator interfaces provide insufficient insight into the status of the process.
In recent years, research has been done to industrial business losses and accidents caused by defective interfaces. The most common cause of errors and accidents was, that the operators did not have the right information to intervene effectively when abnormal situations occurred.
The amount of data available was overwhelming, but lacked the tools for the operators, in order to interpret these data correctly.
Data itself is not information but need context in order to be correctly interpreted. Importantly, the manner in which the context is provided.
In order to give the operator sufficient insight into the status of the process, it is necessary to analyze the HMI design over the years, and to adjust the HMI in such a way that the operator is provided with the correct information.
The study first focuses on the available amount of data and its presentation. Data itself is not information but need context in order to be correctly interpreted. Importantly, the manner in which the context is provided.
The vast majority of the data available is presented as single numerical values on a screen. Corresponding information must be requested or the operator must possess this knowledge. Interpretation and action requires increased mental effort from the operator.
Newly designed elements must provide the correct information to the operator at a glance.
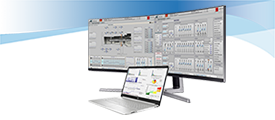
ANSI/ISA – 101.01 Human Machine Interfaces for Process Automation Systems
Analog
Control rooms date back to the earliest days of manufacturing plants. The control rooms consisted of logically grouped instrument panels from which the process was operated. Several process values were plotted for archiving and alarms are presented on separate panels.
Advantage:
- The overall state and health of the process is easy to overlook by a simple walk along the instrument panels.
- Measured values and trends are directly in sight of the operator.
- The alarms were carefully selected and presented individually on a separate panel.
Disadvantage:
- Changes in the process and adding new instruments or alarms have a huge impact on the panels, piping and space and incur high costs.
- Transferring process information to other locations impractical.
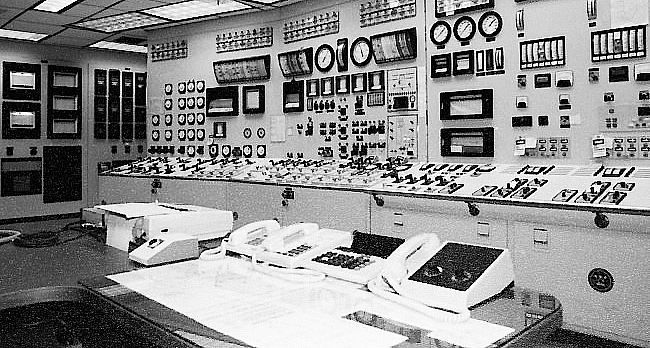
Control room with instrument panels
Data Presentation
The arrival of the Distributed Control System was seen as a major step forward. The signals were monitored by a computerized structure and the instrument panel has been replaced by the displays. Graphic capabilities were limited and, therefore, the displays have been used to present data.
The first interfaces were group displays based on instrument panels. The displays could hold 8-10 blocks of data.
The Operator lost the overview of the process and had to switch between multiple displays to get insight of the process status. In order to draw the attention of the operator for changing conditions of the process outside the field of vision, more and more alarms were configured. A single operator position had about 50 alarms in the instrument panel days. A DCS operator position is now configured with over 3000 alarms.
Advantage:
- System is flexible, changes in the process and adding data is relatively simple.
- Space saving compared with instrument panels.
- Transfer of process information to other locations possible.
Disadvantage:
- The status of the overall process is only available by navigating through all displays.
- Big increase of configured alarms to warn operators for conditional changes to the process.
- More mental strain on the operator interpreting data.
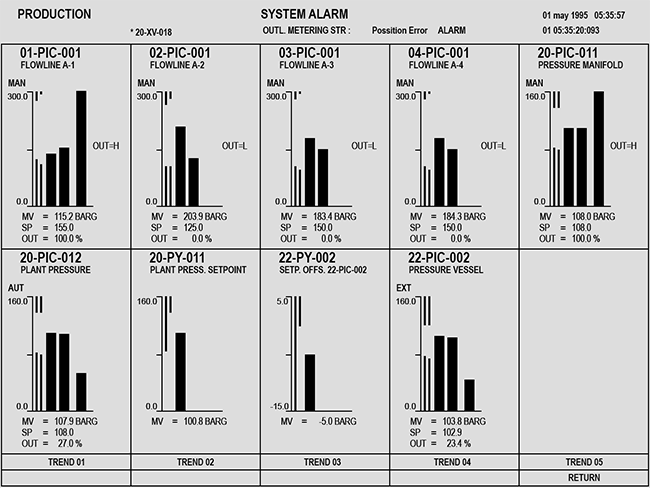
DCS group display
P&ID
The DCS systems evolved rapidly and it became possible to create complex graphics such as lines, equipment and current process values. With improved graphics and color palette available (beginning 8 colors, to date over 16 million colors) it was possible to present conditional changes based on the actual process values.
The new possibilities were used to build displays based on P&IDs. Compared with the group displays this seems to be a major improvement, but the disadvantages, as described previously, are not eliminated.
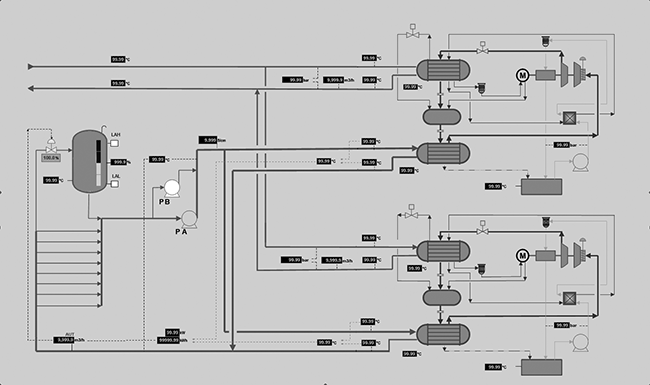
Display based on P&ID
Processes are becoming increasingly complex, and the amount of data is steadily increasing but the operator interfaces are designed on the basis of Examples of 15 to 20 years ago. At a time that little knowledge of proper practices and principles was available.
Due to the large increase in data and displays the risk of misinterpretation increases with all its consequences.
High Performance
The HMI evolution timeline indicates that with the arrival of DCS systems, the advantages of the instrument panels are transformed into disadvantages and vice versa, but despite the evolution of DCS systems, the disadvantages have remained unchanged. Much effort has been expended on the development of systems, but the user side has received little attention.
Correct information is of the utmost importance when making decisions. Current process values are data but without any context no information.
The measured value 21.6 ° C gives the actual temperature, is this too high or too low, is this the optimum temperature or is the limit value almost reached. Everything depends on the knowledge of the operator and the possibility to request additional information. The location on a P&ID based display provides the measurement of any context but requires mental effort from the operator for a correct interpretation.
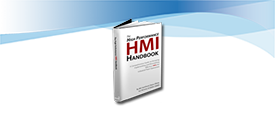
Bill Hollifield, Dana Oliver, Ian Nimmo & Eddie Habibi
High Performance HMI handbook. ©2008 by PAS
Research has shown that humans are very visually oriented. The older analog panel meters unify data and context so all needed information for the operator is determined at a glance.
Based on this new dynamic analog elements have been developed which provide the operator with all the necessary information without having to perform additional operations.In these analog elements data and context are combined.
As an example, the moving analog indicator:
Composition of Analoge Indicator
The following example illustrates the difference between a conventional, P&ID-based display with various measurements and a display where the same measurements are visualized using the newly developed analog elements.
At a glance, it is clear whether the measurements are within the desired operational range, which values require attention, and which may need adjustment.
Compressor HMI P&ID style vs. High Performance
Various process units can be presented by means of the newly developed analogue elements. By placing several process units that make up a production line on a display. The operator will be provided of a clear overview of the current situation of the manufacturing process.
The advantage of former instrument panels, namely; the overall state and health of the process is determined at a glance is herewith incorporated in the DCS system.
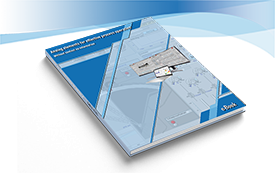
analog context.pdf