HMI Evolution
Many processes were automated 15 years or more ago at a time when process automation was still in its infancy. A lot has changed in the meantime; hardware is outdated and computer systems are evolved. The support for the outdated hardware and software has stopped.
For many companies, the time has come to replace the outdated systems, either in its totality or in phases. In both cases, the largest part of the available budget is spent on "state of the art" hardware and software. The rest of the budget is spent to transfer the existing HMI to the new operating system. For reasons of time and money the existing HMI is converted by means of a, usually available, migration application.
Result: A Hypermodern, multimillion dollar facility that is operated from an HMI that was developed decades ago on the basis of the limited knowledge, brief guidelines and limited possibilities.
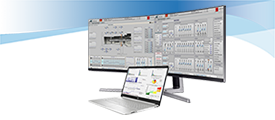
ANSI/ISA-101
Since the arrival of Distributed Control Systems, production processes have been extensively automated. The automation allows the production processes to be more effective and increases the efficiency. The automated processes are constantly monitored and controlled on the basis of reaction (intervention) in abnormal situations such as; low alarms, high alarms or faults. Despite the enormous development in the computer industry and the extensive automation, the production yield has not increased equally and the downtime, as well as the number of accidents, has not been drastically reduced. Research has shown that a change in the way of process operation is necessary, from reactive to proactive.
Proactive means that the operator must at all times be aware of the current situation and based on the right information, adjust the process before an abnormal situation occurs. In order to provide the operator with the right tools for correctly interpreting all available data, it is necessary to review the HMI. New guidelines have been drawn up for the design, implementation and maintenance of Human Machine Interfaces for Industrial Plant Operations. With the help of these guidelines, the available data is presented in such a way that the operator is enabled to run the process as smooth and efficient as possible. The new guidelines are an important basis in HMI development.
ANSI/ISA-101
In recent years, research has been carried out into industrial business losses and accidents caused by faulty interfaces. Based on the research, new guidelines have been drawn up for the design, implementation and maintenance of Human Machine Interfaces for Industrial Plant Operations in the standard:
ANSI/ISA – 101.01 Human Machine Interfaces for Process Automation Systems.
The HMI designed according to this guideline is also known as High Performance HMI.
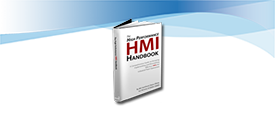
Bill Hollifield, Dana Oliver, Ian Nimmo & Eddie Habibi
High Performance HMI handbook. ©2008 by PAS
In the development phase of the guidelines, the Abnormal Situation Management consortium (ASM), in collaboration with Nova Chemicals, conducted a study into improved process control based on High Performance HMI.
In this study, twenty-one experienced operators were tested using traditional process displays versus process displays designed in accordance with the High Performance guidelines. Using an advanced simulator, operators had to detect and respond to identical faults and abnormal situations.
The results were clear. Using the High Performance HMI, more operators could consistently detect abnormal situations long before an alarm was triggered.The situations were handled in much less time and with a much higher success rate.
Task |
Traditional HMI |
High Performance HMI |
Result |
---|---|---|---|
Detecting abnormal situations before alarms occur. | 10% of the time | 48% of the time | A 5x increase |
Success rate in handling abnormal situations. | 70% | 90% | 37% over base case |
Time to complete abnormal situation tasks. | 18,1 minutes | 10,6 minutes | 41% reduction |
The result related to historical incident figures represents an annual saving of $ 800,000 for 1 ethylene plant, by switching to High Performance HMI.
The result of the study shows that it is worthwhile to evaluate the existing HMI and to adapt it with the help of the new guidelines.
Optimization
In view of all developments in the process industry, it is important to adapt the HMI according to the latest guidelines not only for new projects but also for migration projects. Conversion can play an important role in this, not as an end result but as a starting point. The advantage of converting is not only that the existing layout but also all I/O is transfered.
After the conversion, dynamic elements can be replaced or added and colors can be changed. Embedded trends and links to trend, info and/or parameter displays can be added. The outdated HMI is optimized by relatively small interventions and meets the guidelines. This has improved the information provision and reduced the use of color. The operator is therefore better supported in interpreting the process and taking decisions. This reduces stress and fatigue.
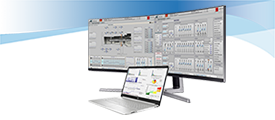
To illustrate, an example of an ultrafilter display after conversion and after optimization. The optimized display contains the same I / O as the converted display, the dynamic elements have been replaced by High Performance elements. There is a clear separation in cleaning and production.
Ultrafilter cleaning additional info:
- Type of cleaning
- Chemicals used
- Cleaning status
- Links for direct access to various settings displays for cleaning.
Ultrafilter production additional info:
- Production status
- Embedded trend transmembrane pressure
- Adjustable trend timespan
- Links for direct access to various settings displays and trend displays for production.
Ultrafilter display na conversie.
Ultrafilter display na optimalisatie.
Optimization
The extensive automation of production processes also has consequences for the HMI. To make the production process as smooth and efficient as possible, a change of process control is necessary, from reactive to proactive. In order to assist the operator in the proactive operation of the process, new elements have been developed for designing a new HMI or optimizing the existing HMI.
When the time has come to replace outdated systems, it is advisable to evaluate and optimize the existing HMI, so that optimal use can be made of the possibilities offered by the new hardware and software.
Conversion offers the possibility to convert the existing HMI to the new operating platform in a short time. Then the converted HMI serves as the basis for the optimization process.
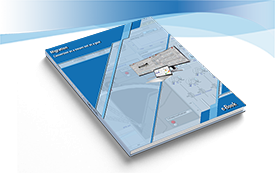
download artikel:
HMI Migration.pdf